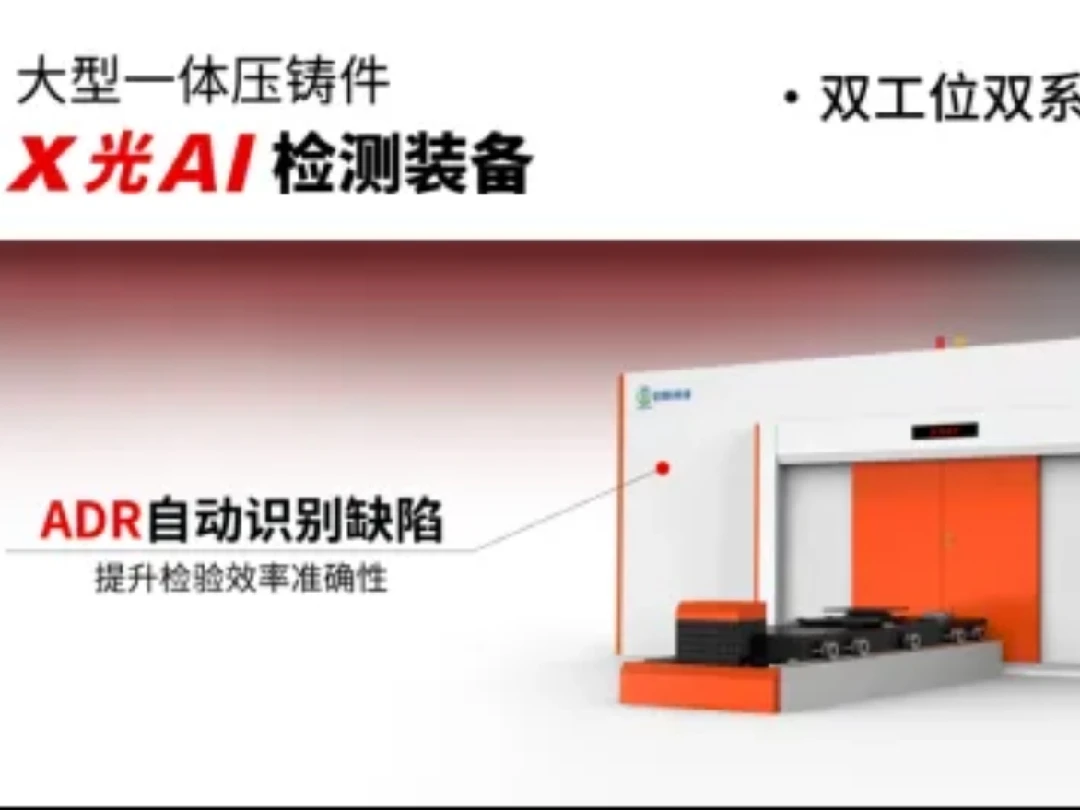
X射线检测技术:新能源汽车安全的守护者


引言:新能源汽车的崛起与质量挑战
近年来,新能源汽车(NEV)凭借环保、高效的优势迅速占领市场,成为全球汽车产业转型的核心方向。然而,随着动力电池能量密度的提升、车身轻量化材料的普及以及电子元器件的复杂化,如何保障核心部件的安全性和可靠性,成为行业亟待解决的难题。在这一背景下,X射线检测技术以其“透视万物”的能力,悄然成为新能源汽车产业链中不可或缺的“质量守门员”。
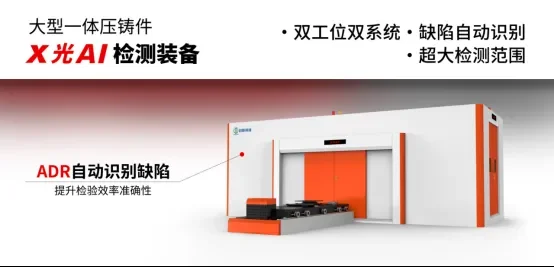
一、为何X射线检测对新能源汽车至关重要?
新能源汽车的核心技术围绕“三电系统”(电池、电机、电控)展开,而传统检测手段(如目检、超声波检测)往往存在局限性:
电池安全隐患:锂离子电池内部的极片对齐度、焊接质量、微裂纹等缺陷可能引发热失控,但肉眼或常规手段无法精准识别。
轻量化材料检测:碳纤维、铝合金等材料的内部孔隙、分层问题直接影响车身结构安全。
电子元器件封装:IGBT芯片、高压线束的连接若存在虚焊或气泡,将导致电路故障甚至起火。
X射线检测凭借高分辨率、非破坏性等特点,可穿透材料表层,直接呈现内部结构的3D图像,成为解决这些痛点的关键技术。
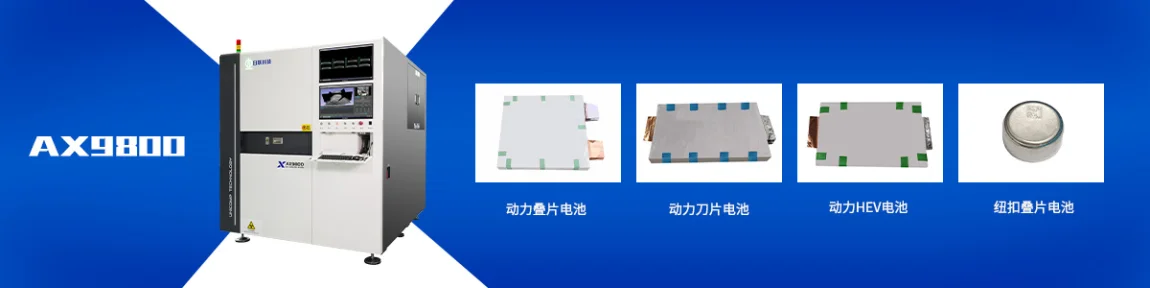
二、X射线检测在新能源汽车中的核心应用场景
动力电池的全生命周期检测
电芯生产:检测极片涂布均匀性、卷绕对齐度,确保电池一致性。
模组封装:识别焊接点气孔、裂纹,避免因接触不良引发的局部过热。
退役电池回收:评估电池内部老化程度,为梯次利用提供数据支持。
电机与电控系统的精密检测
定子绕组的绝缘层完整性、转子磁钢的装配精度,均可通过X射线实时成像定位缺陷。
电控系统PCB板的焊点质量、线路短路问题一览无余,显著降低故障率。
车身结构与高压零部件的质量控制
轻量化材料的内部缺陷(如孔隙率)直接影响碰撞安全性,X射线可量化分析并优化生产工艺。
高压连接器的插针接触状态、密封性能检测,确保高压系统稳定运行。
案例:某头部电池企业采用微焦点X射线CT技术,将电池内部缺陷检出率从85%提升至99.9%,大幅降低售后风险。
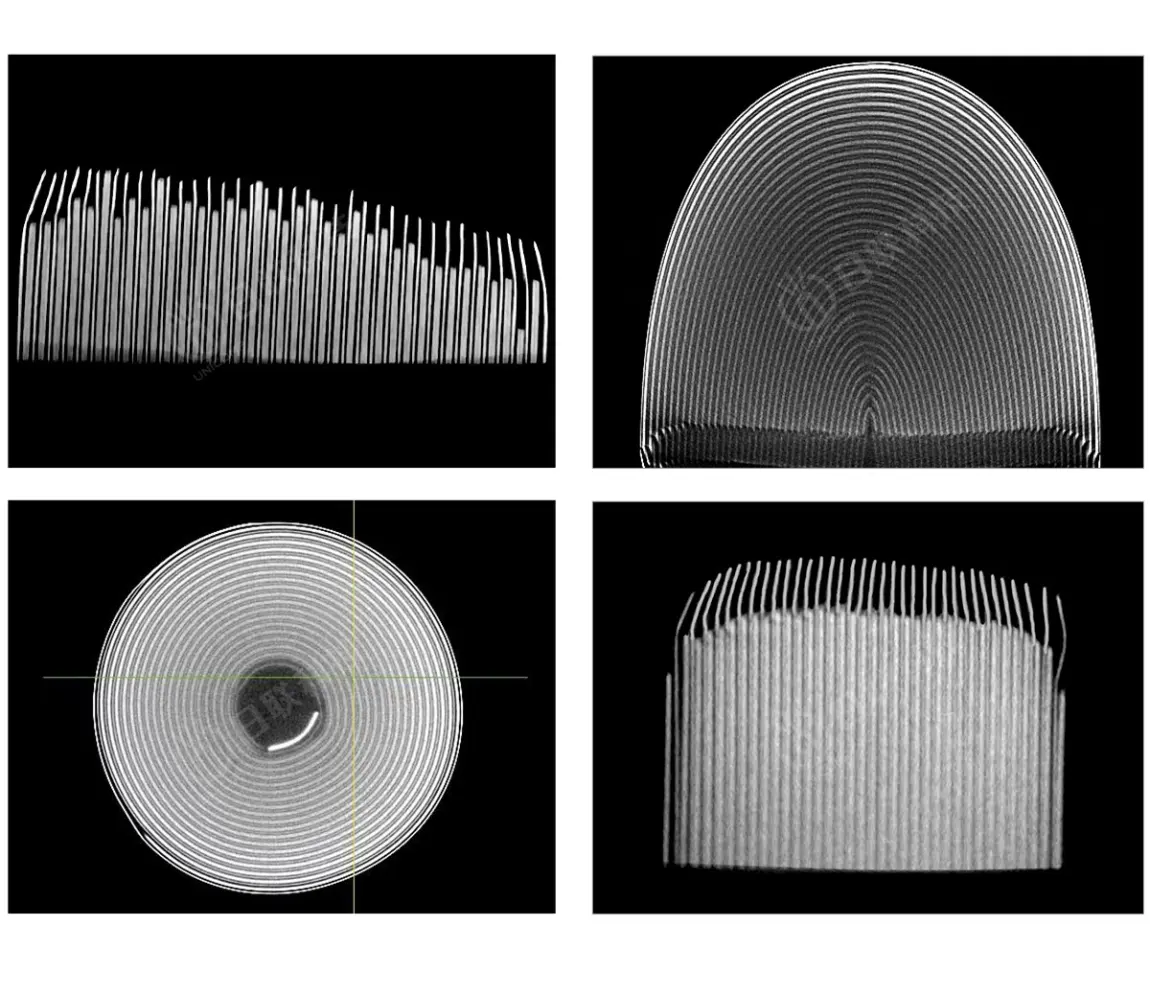
三、技术升级:X射线检测的智能化未来
随着人工智能和工业互联网的融合,X射线检测正从“人工判读”迈向“智能诊断”:
AI缺陷识别:通过深度学习模型,系统可自动分类缺陷类型(如裂纹、气泡、异物),并实时反馈至生产线。
云平台协同:检测数据上传至云端,实现跨工厂、跨供应链的质量数据对比与工艺优化。
在线实时检测:高精度X射线设备集成到自动化产线中,实现100%全检,替代传统的抽样检测模式。
行业预测,到2030年,全球新能源汽车X射线检测市场规模将突破50亿美元,复合增长率超过15%。
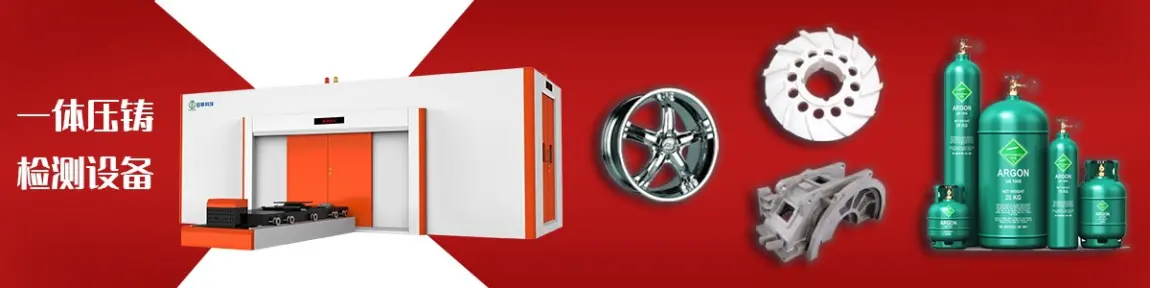
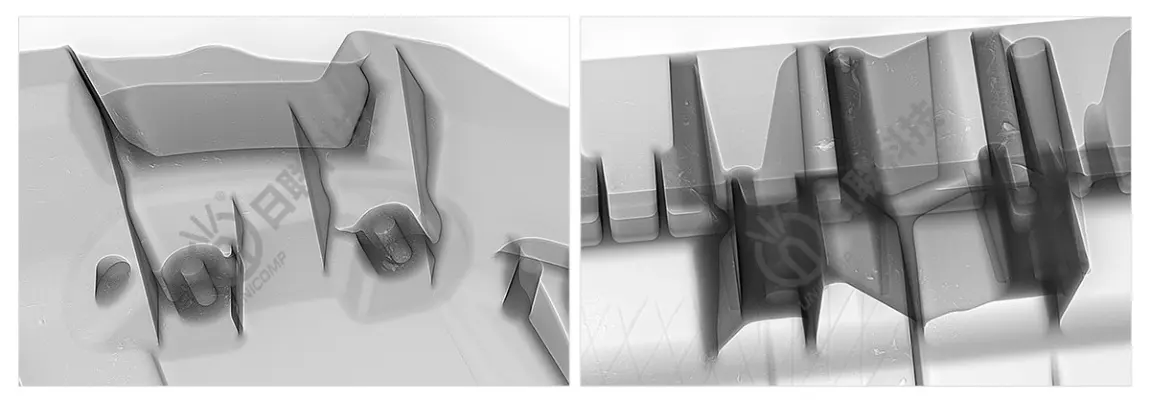
四、挑战与展望
尽管前景广阔,X射线检测技术的普及仍面临挑战:
成本与效率平衡:高精度设备投入高,需通过模块化设计降低中小企业的使用门槛。
辐射安全规范:需建立更严格的操作标准和防护措施,确保人员与环境安全。
多技术融合:与红外热成像、声发射检测等技术协同,构建多维度的质量监控网络。
未来,随着固态电池、一体化压铸等新技术的落地,X射线检测将向更高分辨率、更快成像速度的方向演进,为新能源汽车的安全与性能保驾护航。
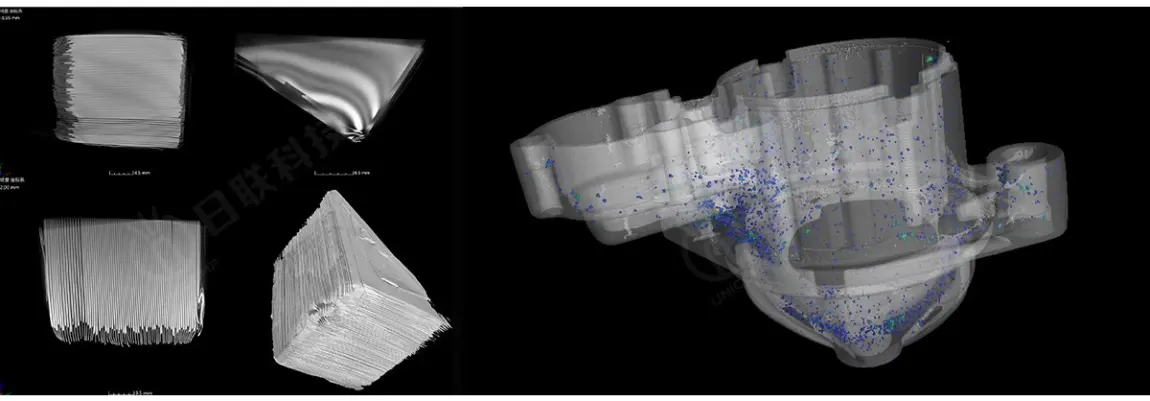
结语:看不见的技术,看得见的未来
在新能源汽车追求“更长续航、更快充电、更高安全”的征程中,X射线检测如同一双“智慧之眼”,穿透表象,直击本质。它不仅是制造端的技术革新,更是消费者对安全信任的基石。当每一块电池、每一辆车的诞生都经过X射线的“深度体检”,或许我们离“零缺陷”的新能源时代,将不再遥远。
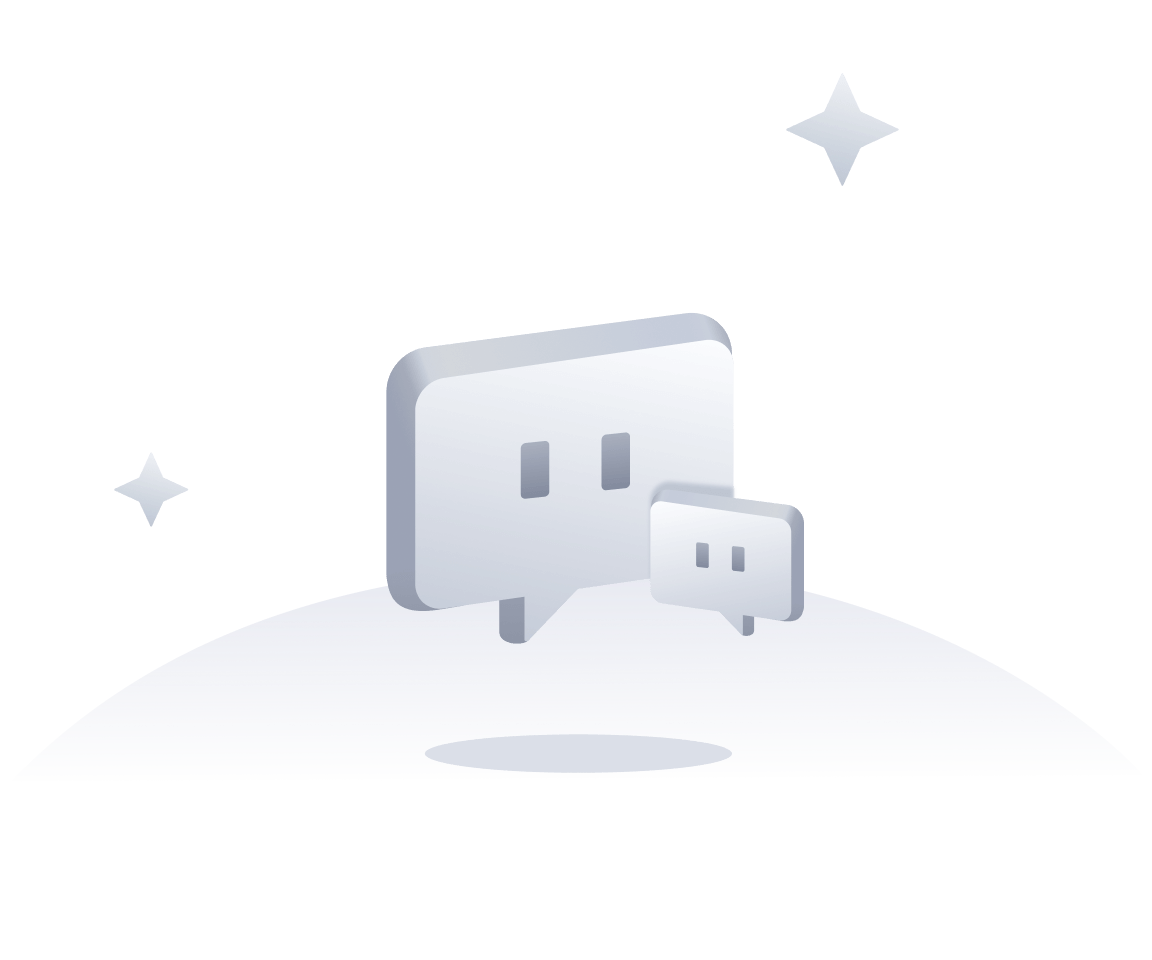